Intelligente transmissies, slim bedraad
Dankzij continu variabele automatische transmissies helpt VDS Getriebe GmbH fabrikanten van voertuigen voor landbouwtoepassingen efficiëntere voertuigen te leveren.
Dankzij continu variabele automatische transmissies helpt VDS Getriebe GmbH fabrikanten van voertuigen voor landbouwtoepassingen efficiëntere voertuigen te leveren. De versnellingen maken gebruik van gepatenteerde, modulaire elementen die specifiek voor elk model zijn ontwikkeld. Ze vormen mechatronische eenheden met aandrijfbeheer van de motor naar het stuurwiel. Sinds de zomer van 2014 worden de elektrotechnische componenten ontwikkeld met EPLAN Electric P8 voor de aanmaak van schema's en met EPLAN Harness proD voor de kabelbomen. Dankzij deze geïntegreerde 3D-tool vinden de mechanische en technische ontwikkeling parallel plaats, waardoor de doorlooptijd veel korter wordt.
Wie al eens in een auto met continu variabele transmissie heeft gereden, kent het gevoel: je kunt non-stop versnellen van stilstand tot maximumsnelheid, zonder te hoeven schakelen. Doordat de motoroutput bij elke snelheid consistent van de verbrandingsmotor naar de wielen wordt overgedragen, is de bestuurbaarheid optimaal. Hiervoor zijn versnellingen nodig waarvan de transmissieverhouding continu kan worden aangepast.
Nooit meer schakelen
Al zolang gemotoriseerde voertuigen worden gemaakt, wordt er geprobeerd versnellingen te ontwerpen die continu variabel zijn. Dat is meer dan alleen een kwestie van rijcomfort. Vooral in domeinen zoals de landbouwsector, waar voertuigen onder extreme omstandigheden en met veel weerstand werken, kan de onderbreking van de vermogenstransmissie door het schakelen tot verlies van grip leiden. Slippartijen of vastzittende wielen kunnen dan het gevolg zijn. “De tijd is rijp voor efficiënte aandrijfsystemen. Niet alleen voor auto's en vrachtwagens, waar het streven naar brandstofbesparing tot steeds complexere systemen leidt, maar ook voor bouw- en werkmachines”, aldus ingenieur Heinz Aitzetmüller. Deze ontwikkelaar van continu variabele automatische transmissiesystemen (CVT) richtte in 2009 de Oostenrijkse firma VDS Getriebe GmbH op in Wolfern, bij Steyr (Oostenrijk). “Voor tractoren zijn al jaren continu variabele transmissies met een hydrostatisch-mechanische aandrijfsplitsing op de markt. Die tonen elke dag opnieuw aan dat continue variabiliteit niet ten koste hoeft te gaan van de efficiëntie.” Aitzetmüller weet waar hij het over heeft, want voordat hij VDS (Variable Drive Systems) oprichtte, was hij zelf betrokken bij de ontwikkeling van zulke transmissiesystemen. “In dit domein bestaan er geen standaardproducten. VDS ontwikkelt voor elk specifiek geval de juiste transmissie”, vertelt hij. “Dat is de enige manier om de balans te vinden tussen optimaal vermogensgebruik, maximale brandstofefficiëntie en redelijke productiekosten.”
Mechatronische eenheden
Volgens Aitzetmüller draait alles hier om een evenwichtige relatie tussen de aandrijfonderdelen, waarbij de gesplitste transmissie mechanisch of via de hydrostatische of elektrische variator wordt overgebracht. Alleen als de aandrijving van de motor tot aan het stuurwiel optimaal wordt verdeeld en gecombineerd, kan de eindgebruiker volledig profiteren van de voordelen van deze technologie. Die combinatie en de controle van de transmissieverhouding gebeurt via diverse planetaire transmissies. Een elektronisch aandrijvingsbeheersysteem voert de schakelingen uit en beheerst de variatoren. Proportionele kleppen voor het beheer van de hydrostatische aandrijving en de multiplaatkoppeling, samen met zo'n 20 sensoren die direct aan de draaiende onderdelen bevestigd zijn om de snelheid en de druk te volgen, maken de gepatenteerde VTP- en VPD-transmissies tot complexe mechatronische eenheden.
Gezocht: een mechatronisch instrument
“Toen het 'alleen' ging om de bedrading van de transmissie zelf – waarbij de bedieningseenheid extern, als een ingekapselde eenheid, was bevestigd – en de klant de overstap naar serieproductie maakte, ontwierpen we de kabelbomen zuiver mechanisch”, vertelt ingenieur Jürgen Fehringer, Hoofd Software bij VDS. “Maar toen een klant ons vroeg om de transmissie, de bedieningseenheid en dus ook de bedrading voor de volledige aandrijflijn van zijn voertuig met vierwielaandrijving te ontwerpen met het oog op serieproductie, werd het ons duidelijk dat onze ontwerpinstrumenten aan vernieuwing toe waren.” “Ons doel was een mechatronisch instrument te vinden waarmee we kabelbomen in 3D konden ontwikkelen, uitgaand van de schema's en het mechanisch ontwerp”, vertelt ontwerpingenieur Davidson Pilsner. “We waren er vanaf het begin af aan van overtuigd dat dure prototypes en/of mislukte pogingen vermijdbaar waren dankzij 3D-modellen. Op die manier kan de ontwikkeling snel worden uitgevoerd, zonder in te leveren op kwaliteit.” “Er waren verrassend veel geschikte softwareprogramma's voorhanden”, herinnert Davidson Pilsner zich. Zo bestaat er een geschikt add-on-product voor het intern gebruikte machinebouwsysteem 3D-CAD. “Gezien de complexiteit en de prijs lijkt dat product echter meer geschikt voor de bedrading van complete vliegtuigen binnen wereldwijde teams”, zegt Jürgen Fehringer met een glimlach. “Toen ik in de lente van 2014 op het internet op onderzoek was, kwam ik EPLAN Harness proD tegen. Dat is een product dat beter op ons 22-koppig bedrijf is afgestemd.”
Elektrisch ontwerp op basis van de schema's
Met EPLAN Harness proD kregen de technici van VDS een bijzonder handig hulpmiddel in handen voor efficiënte 3D-ontwikkeling van kabelbomen. De software combineert de data uit het mechanische en het elektrische ontwerp in een enkel systeem. Van doorslaggevend belang was de mogelijkheid om het elektrotechnische gedeelte van de productontwikkeling te beginnen door EPLAN Electric P8 in de schema's op te nemen en gedurende de rest van het ontwerpproces continu toegang te houden tot gestandaardiseerde elektrotechnische data. De presentaties, waarin rechtstreeks naar de specifieke taken van VDS werd verwezen, waren overtuigend. En dus werden EPLAN Electric P8 en EPLAN Harness proD in de zomer van 2014 geïnstalleerd. “Na een basisopleiding vergeleek ik het product opnieuw met de alternatieven, gebruikmakend van de nieuwe kennis die ik had opgedaan”, vertelt Davidson Pilsner. “Die vergelijking bevestigde dat we de juiste beslissing hadden genomen. EPLAN Harness proD biedt op vrijwel alle vlakken aanzienlijk meer soepelheid.”
Consistente data zonder dubbele invoer
De workflow is duidelijk gestructureerd: allereerst worden de schema's en de bijbehorende materiaallijsten opgesteld in EPLAN Electric P8. Meestal doet Jürgen Fehringer dit. Die data worden vervolgens via XML doorgestuurd naar Davidson Pilsner, die voornamelijk met EPLAN Harness proD werkt. In de kabelboomsoftware worden de data dan gekoppeld aan de informatie uit het mechanische systeem. “Die importprocedure kan waar nodig worden herhaald. Dit betekent dat je een enorme hoeveelheid handmatig databeheer achterwege kunt laten – vooral wanneer je in een later stadium iets aan de elektronica verandert”, stelt hij tevreden vast. “Het resultaat is dat alle data gegarandeerd dezelfde zijn: inconsistenties en fouten zijn op dit vlak zo goed als uitgesloten.” De mogelijkheid om data van connectoren en andere componenten uit de fabriekscatalogi te importeren, bespaart eveneens een hoop werk en helpt fouten te vermijden. Hetzelfde geldt voor de output aan lengtematen, diameters en etiketteringsinformatie voor de individuele kabels en draden. Die kunnen als pdf's worden geproduceerd voor in de werkplaats, of als datarecords voor EPLAN Electric P8 of voor de verpakkingsmachines.
Parallelle mechatronische ontwikkeling
Nu het eerste project zonder problemen en binnen de deadline is voltooid, kan nog geen uitspraak worden gedaan over de rechtstreeks bespaarde tijd tijdens het ontwerp van de kabelboom en de spijkerplaten. Beide technici moesten immers nog met de nieuwe software leren werken en nieuwe gewoontes aanleren, tegelijk met het werk zelf. Ook de aanzienlijke impact van het hergebruik van eerder ontwikkelde onderdelen ontbreekt in dit eerste project uiteraard. “Het echte nut schuilt in de mogelijkheid om het ontwikkelingsproces van onze complexe mechatronische producten volledig te transformeren”, zegt Jürgen Fehringer. “In het verleden kon de kabelboom pas worden gemaakt nadat het mechanische prototype was voltooid.” Op dat prototype werden metingen uitgevoerd en de kabeltrajecten werden op basis daarvan vastgelegd. Vaak leidde dat tot mechanische aanpassingen, bijvoorbeeld omdat er geen ruimte is voor de kabeldoorvoer. Vandaag kunnen we de kabelboom gelijktijdig en gecoördineerd met het mechanische ontwerp ontwikkelen. Dat betekent dat een heleboel tests op het computerscherm kunnen worden uitgevoerd alvorens de prototypes worden gebouwd. Bovendien kunnen de data ook van EPLAN Harness proD naar het MCAD-systeem worden overgebracht, waardoor bij alle botsproeven automatisch rekening wordt gehouden met de geometrie van de kabelboom. De mechanische en elektrische componenten van het prototype komen tegelijk – en in hun geoptimaliseerde vorm – bij de testbank aan, waar ze worden ‘samengevoegd’ en meteen kunnen worden getest. Heinz Aitzetmüller is hier zeer over te spreken: “Dankzij de parallellisering van de mechatronische productontwikkeling kunnen we onze klanten helpen hun productontwikkeling veel sneller uit te voeren.”
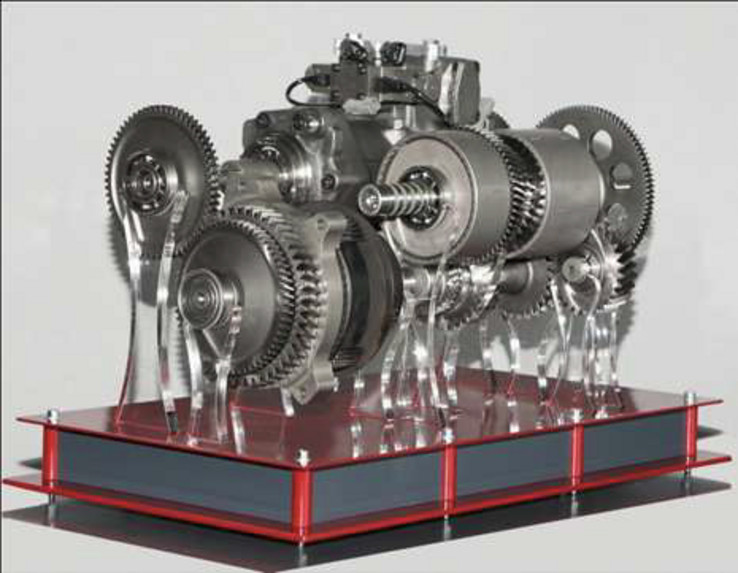
De gepatenteerde continu variabele automatische VTP- en VPD-transmissies van VDS Getriebe GmbH hebben verbeterde efficiëntie van landbouw- en gemeentelijke nutsvoertuigen tot doel. © VDS