Des engrenages intelligents et intelligemment reliés
Avec des transmissions automatiques à variation continue, VDS Getriebe GmbH aide les fabricants de véhicules utilitaires agricoles et municipaux à augmenter l’efficacité et la durée de vie de ces derniers.
Avec des transmissions automatiques à variation continue, VDS Getriebe GmbH aide les fabricants de véhicules utilitaires agricoles et municipaux à augmenter l’efficacité et la durée de vie de ces derniers. En utilisant des éléments modulaires brevetés spécifiquement développés pour le modèle, les transmissions sont des unités mécatroniques avec gestion de l’entraînement, qui s’étendent du moteur jusqu’au moyeu. Depuis l'été 2014, des composants électrotechniques ont été développés avec EPLAN Electric P8 pour la création de schémas et avec EPLAN Harness proD pour les faisceaux de câbles. L’outil 3D intégré permet d’assurer le développement mécanique et électrique en parallèle, garantissant ainsi une réduction considérable du temps de mise sur le marché.
Si vous avez déjà conduit une voiture équipée d’une transmission à variation continue, vous connaissez alors le sentiment que l’on ressent de pouvoir accélérer sans interruption de l’arrêt à la vitesse maximale sans changer une seule vitesse. La transmission régulière de la puissance du moteur depuis le moteur à combustion jusqu’aux roues, à toutes les vitesses, assure un plaisir de conduite optimal. Cela nécessite des vitesses dont le rapport de transmission peut être adapté en continu.
Ne changez plus jamais de vitesse
Depuis que des véhicules à moteur sont produits, diverses tentatives se sont succédées pour concevoir des engrenages qui soient à variation continue. Il s'agit bien plus que d’un simple confort supplémentaire pour le conducteur. Particulièrement dans des domaines tels que l’agriculture où les véhicules fonctionnent dans des situations extrêmes, avec des frictions atteignant le seuil, l’interruption de transmission de la puissance via les changements de vitesse peut mener à des enrayages. Le risque est alors le dérapage ou le blocage. « Le moment est venu pour des systèmes de transmission efficaces. Pas uniquement pour les véhicules et poids lourds, dans lesquels la recherche en matière d'économies sur la consommation de carburant produit des systèmes toujours plus complexes, mais également pour le bâtiment et les machines de travail », explique Heinz Aitzetmüller. Il se consacre au développement de transmissions automatiques à variation continue (CVT) et a fondé VDS Getriebe GmbH à Wolfern, près de Steyr (Haute Autriche) en 2009. « Dans les tracteurs, les transmissions à variation continue combinant puissances hydrostatique et mécanique sont commercialisées depuis des années et prouvent quotidiennement qu’efficacité et variation continue ne sont pas contradictoires. » Heinz Aitzetmüller sait ce dont il parle. En effet, il s’est largement impliqué dans le développement de ces transmissions chez son précédent employeur, avant la création de VDS (Variable Drive Systems). « Il n’existe aucun produit standard dans ce domaine. VDS développe les transmissions appropriées pour chaque cas spécifique », explique-t-il. « Il s’agit du seul moyen de créer un équilibre entre l’utilisation optimale de la puissance, une efficacité maximale du carburant et des coûts de fabrication raisonnables. »
Unités mécatroniques
Selon Heinz Aitzetmüller, ce qui est primordial dans ce cas, c’est une relation équilibrée entre les éléments de puissance qui, dans les transmissions à division de puissance, sont transmis mécaniquement ou via le variateur hydrostatique ou électrique. Seule la combinaison optimale des dérivations de puissance du moteur jusqu’au moyeu permet au client final de profiter pleinement de l’avantage de la technologie. La fusion des dérivations de puissance et le contrôle du rapport de transmission surviennent via plusieurs transmissions à trains planétaires. Un système électronique de gestion de la transmission effectue les changements de vitesse et contrôle les variateurs. Les valves proportionnelles contrôlant l’entraînement hydrostatique et les embrayages multidisques, associés à près de 20 capteurs directement fixés aux composants mobiles pour enregistrer les vitesses et les pressions, font de ces transmissions VTP et VPD brevetées des unités mécatroniques complexes.
Recherché : outil mécatronique
« Tant qu’il s’agissait « seulement » du câblage de la transmission elle-même (l’unité de commande est fixée à l’extérieur sous la forme d’une unité encapsulée) et que la transition vers la production en série était réalisée par le client, nous concevions les faisceaux de câbles de manière purement mécanique », explique Jürgen Fehringer, directeur des logiciels chez VDS. « Lorsqu’un client nous a demandé de développer la transmission, l’unité de commande et, par conséquent, le câblage de l’intégralité de la transmission de son véhicule municipal tout-terrain jusqu’à la production en série, il était évident que nous devions mettre à niveau nos outils de conception. » « Notre objectif était de trouver un outil mécatronique permettant de développer les faisceaux de câbles en 3D sur la base d'un schéma et de la conception mécanique », relate l’ingénieur concepteur Davidson Pilsner. « Depuis le tout début, nous étions persuadés que pour éviter les prototypes onéreux et/ou des tentatives vaines, nous devions uniquement travailler avec des modèles 3D afin que le développement puisse être effectué pendant le peu de temps imparti, sans perdre en qualité. » « Le choix d’outils logiciels appropriés était incroyablement vaste », se souvient Davidson Pilsner. Parmi ces options, il était possible d’obtenir un produit complémentaire approprié au système de CAO en 3D de l’ingénierie mécanique. « Mais du fait de sa complexité et de son prix, il semblait plus approprié à la construction du câblage pour un avion complet par des équipes internationales », sourit Jürgen Fehringer. « Au cours de mes recherches sur Internet au printemps 2014, je suis tombé sur EPLAN Harness proD, un produit bien mieux adapté à la taille de notre entreprise de 22 employés. »
Une conception électrique à partir du schéma
Avec EPLAN Harness proD, les techniciens de VDS ont découvert un outil extrêmement pratique pour le développement efficace en 3D d’un faisceau de câbles combinant les données des conceptions mécanique et électrique en un seul système. L’un des principaux facteurs décisifs a été l’option permettant de débuter la partie électrotechnique du développement de la production en créant le schéma par combinaison avec EPLAN Electric P8, puis en conservant l’accès aux données normalisées de l’ingénierie électrique pendant le reste de la conception. Les présentations avec référence directe aux tâches spécifiques de VDS ayant été convaincantes, la décision fut prise d’installer EPLAN Electric P8 et EPLAN Harness proD au cours de l’été 2014. « Après une formation basique, j’ai à nouveau comparé le produit avec des alternatives en m’appuyant sur les connaissances que j’avais acquises », explique Davidson Pilsner. « La comparaison a confirmé la justesse de la décision. Pour pratiquement chaque point, EPLAN Harness proD permet un travail considérablement plus fluide. »
Des données cohérentes sans double entrée
Le processus est clairement structuré : au départ, le schéma et les listes de matériaux résultantes sont compilés dans EPLAN Electric P8, normalement par Jürgen Fehringer. Ces données sont ensuite transférées via une interface XML à Davidson Pilsner, qui travaille principalement avec EPLAN Harness proD. Dans le logiciel des faisceaux de câbles, les données sont ensuite associées aux informations du système mécanique. « Cette procédure d’importation pouvant être répétée autant de fois que nécessaire, la gestion manuelle des données n’est pas démesurée, notamment dans le cas de modifications ultérieures apportées aux données électriques », affirme-t-il gaiement. « Il est ainsi garanti que toutes les données sont les mêmes ; les incohérences et les erreurs causées de ce fait peuvent être pratiquement exclues. » L’option d’importation des données des connecteurs et d’autres composants à partir des catalogues du fabricant réduit aussi grandement le travail et supprime les sources d’erreurs. Le même principe s’applique au volume d’informations relatives aux longueurs, sections transversales et de marquage pour les câbles et fils individuels. Elles peuvent être générées au format PDF pour l’atelier ou sous forme de jeux de données pour EPLAN Electric P8 ou pour les machines de conditionnement.
Développement mécatronique parallèle
Une fois le premier projet terminé sans aucune difficulté et dans le respect du délai imparti, aucune déclaration n’a pu être faite à propos du gain de temps direct réalisé lors de la conception du faisceau de câbles et des panneaux. Les deux techniciens ont en effet dû se familiariser avec les nouveaux outils logiciels et ont dû développer des routines tout en réalisant leur travail actuel. Les effets considérables de la réutilisation des pièces précédemment conçues manquent également complètement dans le projet initial. « Le réel effet utile est l’option de transformation intégrale du processus de développement de nos produits mécatroniques complexes », affirme Jürgen Fehringer. « Auparavant, le faisceau de câbles pouvait uniquement être fabriqué une fois le prototype mécanique terminé. » Des mesures étaient prises sur le prototype dans ce but et le routage des câbles était défini sur cette base. Trop souvent, des modifications mécaniques en ont résulté, car il n’y avait pas assez d’espace pour passer les câbles, par exemple. Aujourd'hui, le faisceau de câbles peut être développé simultanément et en coordination avec la conception mécanique. De cette manière, de nombreux essais peuvent être réalisés à l'écran avant que les prototypes ne soient construits. En outre, les données peuvent également être transférées depuis EPLAN Harness proD jusqu’au système de conception mécanique assistée par ordinateur de manière à ce que la géométrie du faisceau de câbles soit automatiquement prise en compte dans tous les essais de collision. Les composants mécaniques et électriques du prototype atteignent simultanément le banc d’essai, déjà dans leur forme optimisée, où ils sont combinés et immédiatement disponibles pour les essais. Heinz Aitzetmüller parle ainsi de l’effet plaisant : « Grâce à la mise en parallèle du développement du produit mécatronique, nous pouvons aider nos clients à réduire radicalement leur délai de développement du produit. »
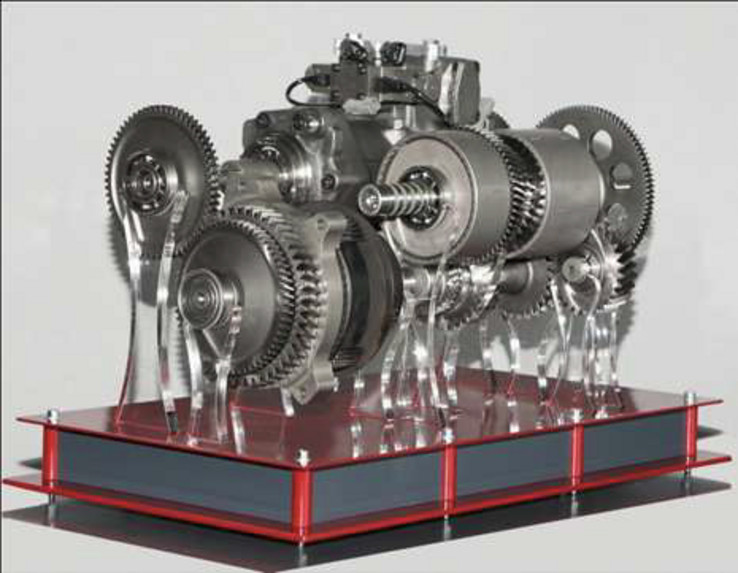
L’amélioration de l’efficacité des véhicules utilitaires agricoles et municipaux est l’objectif des transmissions automatiques à variation continue VTP et VPD brevetées produites par VDS-Getriebe GmbH.
© VDS
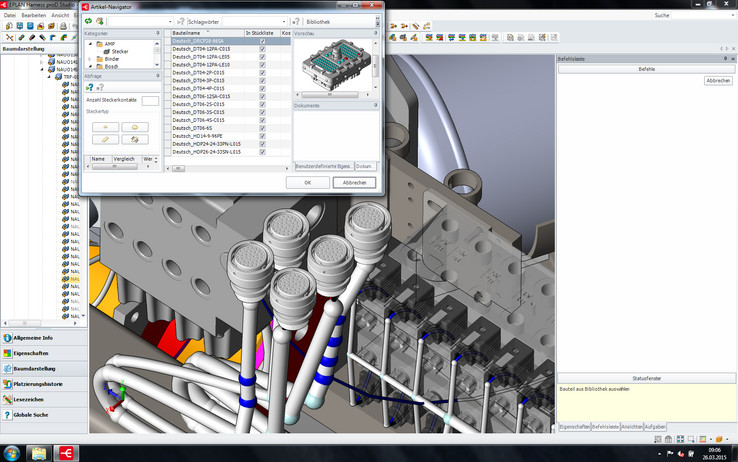
Le faisceau de câbles est développé dans EPLAN Harness proD avant que ne soit terminé le prototype, et en même temps que la conception mécanique, en étroite coopération avec cette dernière grâce à des données partagées. Les données 3D de tous les systèmes traditionnels de conception mécanique assistée par ordinateur peuvent être importées dans ce but.
© VDS