Paramétrage plutôt que dessin
KWS Saat utilise la plate-forme EPLAN pour fabriquer des machines spécialisées.
La majorité des 4 600 employés de KWS Saat SE sont impliqués dans le développement de nouvelles variétés de semences. Les machines et systèmes complexes requis pour le traitement et la production des semences sont également fabriqués en interne à l’aide de la plate-forme EPLAN, en commençant par les schémas de tuyauterie et d’instrumentation (T&I) qui sont conçus à l’aide du module de préplanification Preplanning. Le principe sous-jacent consiste en un processus de conception interdisciplinaire cohérent, de l’ingénierie mécanique et des processus jusqu’à l’ingénierie électrique et hydromécanique.
Les concepteurs savent comment développer différents types de machines requises pour différents objectifs. Mais comment développer des semences pour produire des betteraves sucrières ou des tournesols ? Les sélectionneurs et chercheurs de KWS, basés à Einbeck (Allemagne), savent exactement comment. L’entreprise a été fondée en 1856 et embauche désormais près de 5 000 personnes à travers le monde. Elle génère un chiffre d’affaires de plus d'un milliard d’euros et est l’un des principaux producteurs de semences au monde. Elle se concentre sur les variétés de semences adaptées au climat tempéré, notamment des betteraves sucrières, du maïs, des céréales et des oléagineux.
Chaque année, KWS lance de nouvelles variétés de semences sur le marché agricole, par exemple des semences qui produisent des rendements supérieurs ou sont résistantes aux pathogènes et aux insecticides. Le processus est très long et peut prendre dix à douze ans entre la boîte de Pétri et un produit commercialisable. Les nouvelles variétés développées doivent d’abord subir des tests intensifs, puis une homologation et être ensuite propagées par des exploitations agricoles partenaires. Les semences sont un produit naturel ; les quantités ne peuvent donc pas être simplement produites à la demande.
Des machines spéciales pour le traitement des graines
Pour transformer des semences en produits commercialisables, une technologie de processus avancée est requise, comme l’ingénierie électrique. Manfred Schaper, concepteur électrique et d’automatisations chez KWS : « À Einbeck, nous exploitons l’usine de traitement de semences la plus moderne au monde. » Le principal service de développement, qui développe également la machinerie pour d’autres sites de KWS, est également situé ici.
Le travail implique la conception très exigeante de machines spécialisées. Par exemple, les systèmes très automatisés pour le traitement des semences de betteraves sucrières combinent les processus de nettoyage, de criblage, de séchage, de classification, d’enrobage avec des composés et d’application d'ingrédients actifs. Des semences hétérogènes sont ainsi converties en grains individuels d’une taille définie. Elles sont ensuite semées très rapidement par des semoirs automatisés à des intervalles d’environ 22 centimètres. Avec KWS, les agriculteurs se voient épargner l’angoisse qui anime les amateurs de jardinage du monde entier : celle que seule une fraction des semences semées apparaisse au printemps. En effet, KWS promet un taux de germination de 98 %.
En quête d’un logiciel d'ingénierie intégrée
Le traitement des semences représente un type de « production de campagne » avec des contraintes temporelles spécifiques, ce qui signifie que les machines doivent être disponibles au bon moment. Outre la conception d'une nouvelle machinerie, la rénovation des systèmes existants fait également partie de l'éventail de tâches qui incombe aux ingénieurs de conception. Manfred Schaper, planificateur électrique, innovations techniques : « Nous adaptons souvent les systèmes existants aux nouvelles exigences. »
Les projets commencent par un schéma de T&I
Les concepteurs de systèmes mécaniques tels que Uwe Domhöver commencent par créer un schéma de T&I du système à construire sur la base de discussions avec le client. Le schéma de T&I d’EPLAN Preplanning est utilisé afin de générer un aperçu graphique du système. Les données relatives aux mesures individuelles et aux postes de consommation, ainsi qu’à l’instrumentation peuvent dès à présent être enregistrées à cette étape. Elles sont ensuite disponibles pour toutes les phases d’ingénierie ultérieures et forment la base d’un processus continu et normalisé.
La pneumatique prédomine
EPLAN n’est pas seulement utilisé pour l’ingénierie électrique, mais également pour la pneumatique. Manfred Schaper : « Nous utilisons beaucoup la pneumatique pour automatiser les systèmes. » EPLAN Fluid est l’outil idéal pour cela : « Nos concepteurs configurent les terminaux de distributeurs sur le portail Festo, envoient un code à Festo, puis récupèrent les données EPLAN correspondantes. Cela fonctionne très bien. »
En termes de CAO, EPLAN Fluid et EPLAN Electric P8 sont étroitement liés pour assurer la cohérence de la conception de la technologie d’automatisation pneumatique. KWS utilise de manière intensive EPLAN Data Portal lors de la sélection de composants, comme les convertisseurs de fréquence. Cela simplifie considérablement le processus de conception en fournissant au processus d’ingénierie complet des données et informations uniformes.
Paramétrage plutôt que dessin
La mise en œuvre d’outils EPLAN a modifié la manière dont les concepteurs travaillent. Manfred Schaper : « Auparavant, nous dessinions. À présent, nous effectuons un paramétrage. » Le paramétrage est populaire également en raison de la charge de travail du service : « Nous nous développons fortement et concevons usine et machines pour divers sites. Les nouvelles solutions logicielles d’EPLAN nous permettent de travailler bien plus efficacement et les concepteurs peuvent se concentrer davantage sur des tâches créatives plutôt que répétitives. » Les processus de conception optimisés permettent également de rendre les solutions accessibles plus rapidement pour les collègues des sites de production individuels.
C’est d’autant plus important que les systèmes de KWS sont extrêmement complexes et que la conception est très détaillée. Le tout premier projet que KWS a conçu en interne à l’aide d’EPLAN était extrêmement détaillé. Manfred Schaper fournit un exemple : « Pour les entraînements, nous avions besoins de calculs de dissipation d'énergie et de vérifications du couple. »
Des armoires de commande complexes, de fortes attentes
Les armoires de commande de KWS mesurent généralement 2,40 à 9 mètres de large et sont décentralisées selon les fonctions et composants du système. Des exigences de protection contre les explosions nécessitent souvent d’être respectées, la majorité des armoires de commande sont donc équipées de systèmes d’extinction. KWS utilise le grand système modulaire Siemens pour la technologie de commande et le portail TIA. Certaines des armoires de commande sont conçues par des prestataires de service qui travaillent ensuite également avec la plate-forme EPLAN.
Concevoir selon le principe de « paramétrage plutôt que tracé » s’est rapidement imposé chez KWS. Et ce, pour de bonnes raisons : c’est un gain de temps et une économie de coûts et il permet un travail de conception continu à travers les différentes disciplines, la base de données centrale étant améliorée à chaque étape.
Étape suivante : conception en 3D de l’armoire de commande
Des préparations sont actuellement en cours pour la mise en œuvre d’EPLAN Pro Panel, qui permettront la conception en 3D de l’armoire de commande. Manfred Schaper a également l’intention d’utiliser davantage les macros, par exemple pour les actionneurs : « Il ne restera ensuite plus aux concepteurs qu’à saisir les paramètres et l’actionneur sera automatiquement sélectionné et inséré dans le schéma de connexion avec toutes les données pertinentes. Cela permet de gagner encore plus de temps : nous insérons les macros depuis un schéma de procédé et le schéma est créé par le système. »
Un projet complémentaire est d’augmenter le nombre d’utilisateurs du service d’EPLAN : « Les techniciens de l’usine aurons ensuite accès, via une tablette ou un ordinateur portable, aux schémas de T&I et à l’ingénierie Electric P8 et hydromécanique. Cela facilite la détection des erreurs et accélère la rectification. »
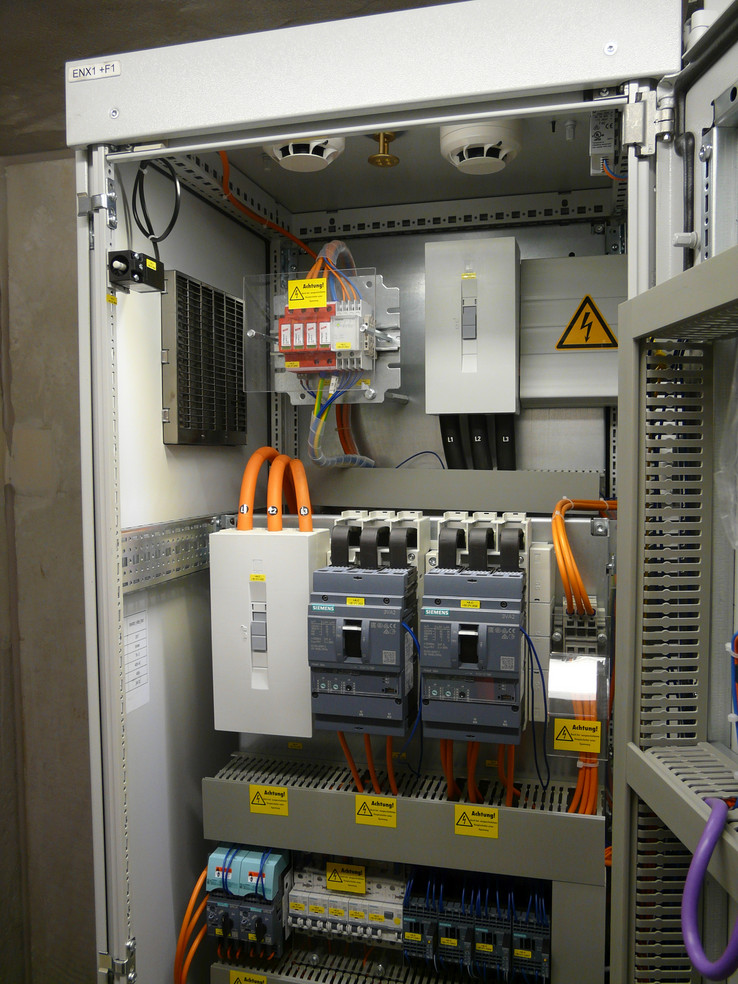
Les armoires de commande, telles que représentées ici dans un exemple de système de filtrage, sont conçues à l’aide d’EPLAN Pro Panel.
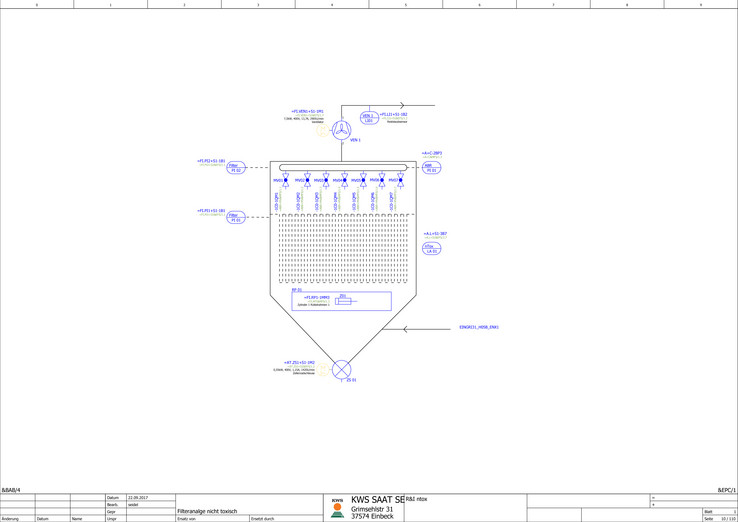
Dans EPLAN Preplanning, la conception de systèmes spéciaux pour le traitement des semences débute par un schéma de T&I.